How Do Drywall Companies Keep Themselves Safe During Drywall Installation
Safety is a paramount concern for drywall companies during installation projects. The nature of drywall work involves various risks, including physical strain, exposure to dust and chemicals, and working at heights.

How Do Drywall Companies Keep Themselves Safe During Drywall Installation
This article explores the strategies and best practices that drywall company employ to ensure the safety of their workers and clients during installation processes.
1. Comprehensive Training and Education
The foundation of safety in drywall installation lies in comprehensive training. Workers are educated about the potential hazards and the proper techniques for handling materials and equipment. This training typically includes the correct ways to lift and secure drywall, minimizing the risk of musculoskeletal injuries.
2. Use of Personal Protective Equipment (PPE)
Drywall companies enforce the use of personal protective equipment. This includes safety goggles to protect the eyes from dust and debris, gloves to protect the hands, masks or respirators to prevent inhalation of harmful dust, and hard hats to protect from overhead hazards.
3. Dust Control Measures
Drywall sanding generates a significant amount of dust, which can be hazardous to respiratory health. Companies use various methods to control dust, such as using dust-extracting sanders, wet-sanding techniques, and ensuring adequate ventilation in the workspace.
4. Ergonomic Tools and Equipment
To reduce physical strain, companies invest in ergonomic tools and equipment. These include drywall lifts to assist in raising and holding panels in place, which helps prevent overexertion and back injuries.
5. Safe Handling and Storage of Materials
Proper handling and storage of drywall sheets are crucial to prevent accidents. Workers are trained to handle sheets safely to avoid dropping or collision. Materials are also stored in stable, secure areas to prevent them from falling or causing obstructions.
6. Regular Maintenance of Tools and Equipment
Regular maintenance of tools and equipment is essential to prevent malfunctions and accidents. This includes checking the condition of ladders, scaffolds, lifts, and power tools and ensuring they are in safe working order.
7. Adherence to Occupational Safety Standards
Drywall companies adhere to occupational safety and health standards set by regulatory bodies. These standards provide guidelines on various aspects of the job, including ladder use, scaffold safety, and exposure limits to certain substances.
8. First Aid and Emergency Preparedness
Companies are equipped with first aid supplies and have procedures in place for emergency situations. Workers are often trained in basic first aid and know how to respond in case of an accident.
9. Client Safety and Communication
Safety extends to the clients as well. Companies ensure that the work area is cordoned off and communicate with clients about potential hazards and safety protocols during the installation process.
Conclusion: How Do Drywall Companies Keep Themselves Safe During Drywall Installation
For drywall companies, safety during installation is not just a regulatory requirement but a fundamental aspect of their operations. By implementing thorough training, enforcing the use of protective equipment, adopting dust control measures, and maintaining tools and equipment, these companies strive to create a safe working environment.
These practices not only protect the workers but also ensure the safety and satisfaction of clients, contributing to the overall success and reputation of the company in the competitive field of construction and renovation.
What Are the Major Differences Between Sheetrock and Drywall
For many, the terms Sheetrock and drywall are often used interchangeably in the construction world. These materials are indeed very similar, but it’s important to know their differences, particularly when undertaking a construction or renovation project.
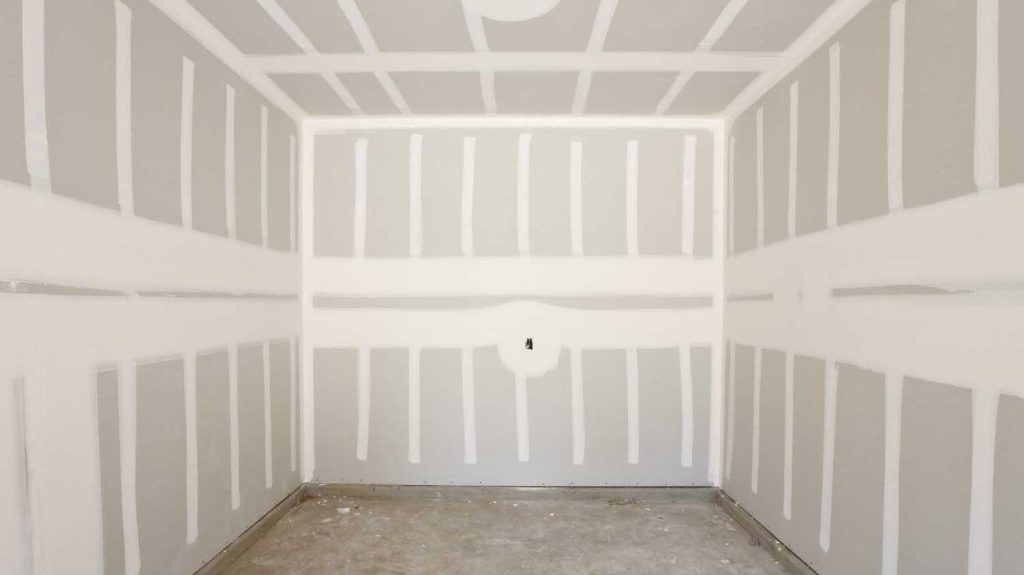
What Are the Major Differences Between Sheetrock and Drywall
This article will unravel the distinctions and similarities between Sheetrock and drywall and some ideas about drywall and sheetrock repair.
Before we dive into the differences, let’s define each term. A drywall is a panel made of gypsum plaster pressed between two thick sheets of paper. It’s used widely in the construction of interior walls and ceilings because it’s quick and easy to install, cost-effective, and fire-resistant.
Sheetrock, on the other hand, is a brand name for drywall produced by the US Gypsum Company. It comes in various forms, including panels and squares, and has different special features depending on the specific type of Sheetrock chosen.
Now, let’s look at their major differences.
The Name:
The primary difference between Sheetrock and drywall lies in their names. Drywall is a generic term for the product, while Sheetrock is a registered trademark of the US Gypsum Company. It’s like how we often use brand names like Kleenex or Band-Aid to refer to a general product category.
Varieties:
Drywall comes in standard forms. The most used drywall panels are 1/2″ thick and come in different sizes for various uses. However, there’s also moisture-resistant drywall, known as green board, and more fire-resistant forms, such as Type X.
On the contrary, Sheetrock offers a range of specialty products. These include Mold Tough Sheetrock, which resists mold growth, Fire code Sheetrock, which has superior fire-resistant properties, and Ultralight Sheetrock, which is lighter and easier to handle than standard drywall.
Quality and Price:
Some builders argue that Sheetrock is of superior quality compared to generic drywall because of its stricter manufacturing process and quality control measures. It’s also noted for its excellent working properties, such as scoring, snapping, and resistance to crumbling. However, this higher quality can come with a slightly higher price tag compared to generic drywall. The cost difference is usually not significant but can add up in large projects.
Availability:
While drywall is produced by numerous companies and available in most hardware stores and construction suppliers, Sheetrock might not be as readily available, especially outside of North America. Some stores may carry the brand, but you may need to place a special order or go to a supplier that specifically carries the Sheetrock line.
Conclusion: What Are the Major Differences Between Sheetrock and Drywall
While Sheetrock and drywall may seem different, the reality is that Sheetrock is a type of drywall. The major differences lie in the name, the variety of products offered, and sometimes, the quality and price. However, for most residential projects, standard drywall and Sheetrock can be used interchangeably. The best choice ultimately depends on the specific needs of your project, your budget, and the products available in your area. Always consult with a construction or renovation professional to determine which product is best suited for your specific project.
What Are the Obvious Signs for Stucco Replacement
Stucco, a mixture of cement, sand, and lime, has been a popular exterior finish for buildings due to its resilience and aesthetic appeal. However, like any other building material, stucco doesn’t last forever.
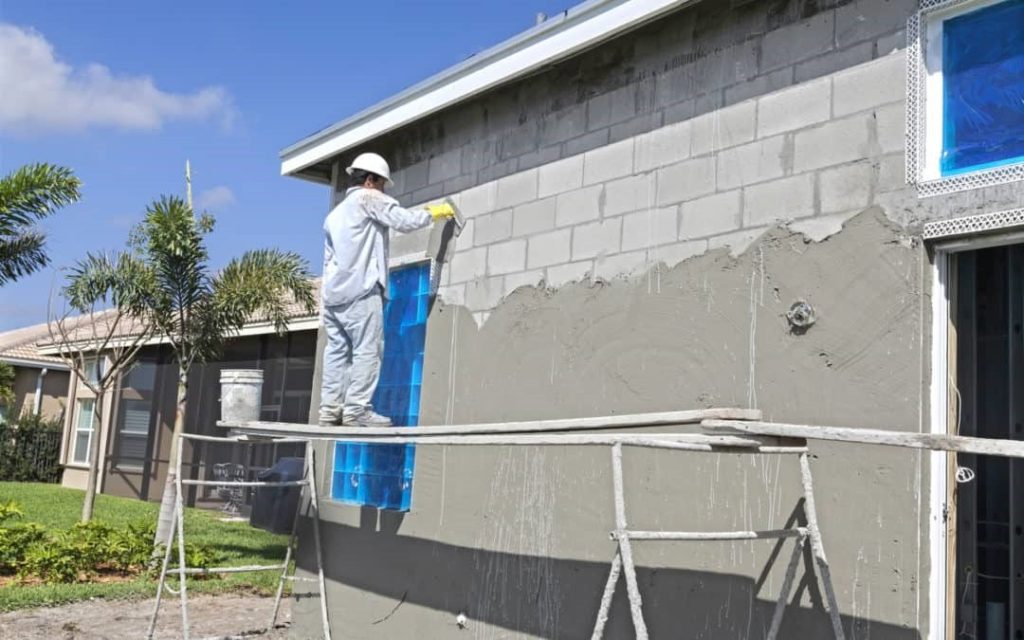
What Are the Obvious Signs for Stucco Replacement
Recognizing the signs that your stucco needs replacement is essential to maintain your building’s structural integrity and curb appeal. This article explores the obvious signs that it might be time to replace your stucco or just a simple stucco repair.
Extensive Cracking:
While minor, hairline cracks in stucco can usually be repaired, extensive cracking is a sign that replacement may be necessary. Large cracks, multiple spiderweb-like cracks, or cracks that reappear soon after being repaired all suggest deeper structural issues that could require a complete stucco overhaul.
Bulging or Warping:
If your stucco starts to bulge, warp, or pull away from the underlying surface, it’s often an indication of water damage. The trapped moisture can cause the stucco to separate from the wall, creating a potential hazard as large sections may eventually fall off.
Water Damage:
Signs of water damage, such as staining, mildew, or mold on your stucco, indicate that water is infiltrating the material. Chronic moisture can compromise the stucco’s integrity, making replacement necessary.
Efflorescence:
Efflorescence—the accumulation of crystalline salt deposits on the stucco surface—indicates that water is moving through the stucco. This water movement can erode the internal structure of the stucco over time, requiring replacement.
Persistent Dampness:
If areas of your stucco remain damp even in dry weather, or if the stucco is soft and crumbles easily, these are strong indicators of water penetration. The persistent moisture could lead to severe structural damage if not addressed.
Severe Discoloration:
While minor staining or discoloration can often be remedied with cleaning or painting, severe or widespread discoloration could signal more serious issues like water intrusion or degradation of the stucco mix itself. If discoloration persists despite efforts to clean or cover it, stucco replacement might be the best option.
Advanced Age:
Stucco typically has a lifespan of 50 to 80 years. If your stucco is within this age range and you’re seeing multiple signs of wear and tear, it might be time for a replacement rather than continually investing in repairs.
Underlying Structural Damage:
If you’re dealing with problems like rot in the building’s underlying wood frame, you’ll likely need to remove the stucco to address the issues. In such cases, replacing the stucco entirely often makes the most sense.
Conclusion: What Are the Obvious Signs for Stucco Replacement
Seeing these signs doesn’t automatically mean you need to replace all the stucco. In some instances, partial replacement or repair may be sufficient. Therefore, it’s crucial to consult with a stucco professional to evaluate the extent of the damage and suggest the best course of action.
In conclusion, while stucco is a durable and attractive exterior finish, it’s not invulnerable. Recognizing the signs of serious stucco issues can help you take timely action, preventing more significant damage to your building. Through vigilant monitoring and proper care, you can ensure your stucco exterior continues to protect and beautify your building for many years.